CONCENTRATORE
AZIENDA: ZANLORENZI SÃO MARCOS
PRODOTTO DA REALIZZARE
Succo d’uva
Siamo partiti da una macchina usata, che è stata completamente smontata e revisionata nella sua interezza:
Abbiamo effettuato:
- Cambio della camera di primo effetto: a causa del cattivo stato di quella esistente.
- Sono state eseguite prove idrauliche nelle camere per verificare che non ci fossero perdite negli Assi dei tubi (parti critiche di interazione tra il vapore e il prodotto).
- Sono stati realizzati tutti gli ingressi necessari per il successivo layout delle tubazioni, come ingressi del vapore, uscite di condensa, uscite di incondensabili, adattamento dell’uscita del prodotto, ricircoli, ecc.
- Tutti i tubi sono stati realizzati a partire da 0 con un rispettivo disegno 3D che ci ha permesso di facilitare la fabbricazione degli stessi.
- Le gambe della struttura sono state allungate per poter sollevare la macchina nella sua interezza per un miglior funzionamento.
- L’intera struttura è stata de-zincata e zincata, in quanto è l’unico elemento che non è in acciaio inox, e a questo scopo sono stati eseguiti trattamenti superficiali sull’acciaio per garantirne la lunga durata senza alcuna perdita di qualità del materiale.
- È stato effettuato un preassemblaggio dell’intera macchina per una corretta fabbricazione e connessione della macchina e per evitare difficoltà al momento dell’assemblaggio della macchina presso il cliente.
Infine, ma non per questo meno importante, sono stati realizzati tutti gli isolamenti necessari per aumentare l’efficienza energetica ed evitare qualsiasi tipo di inconveniente durante la produzione, dato che la finitura superficiale data alla lamiera è molto fragile agli urti.
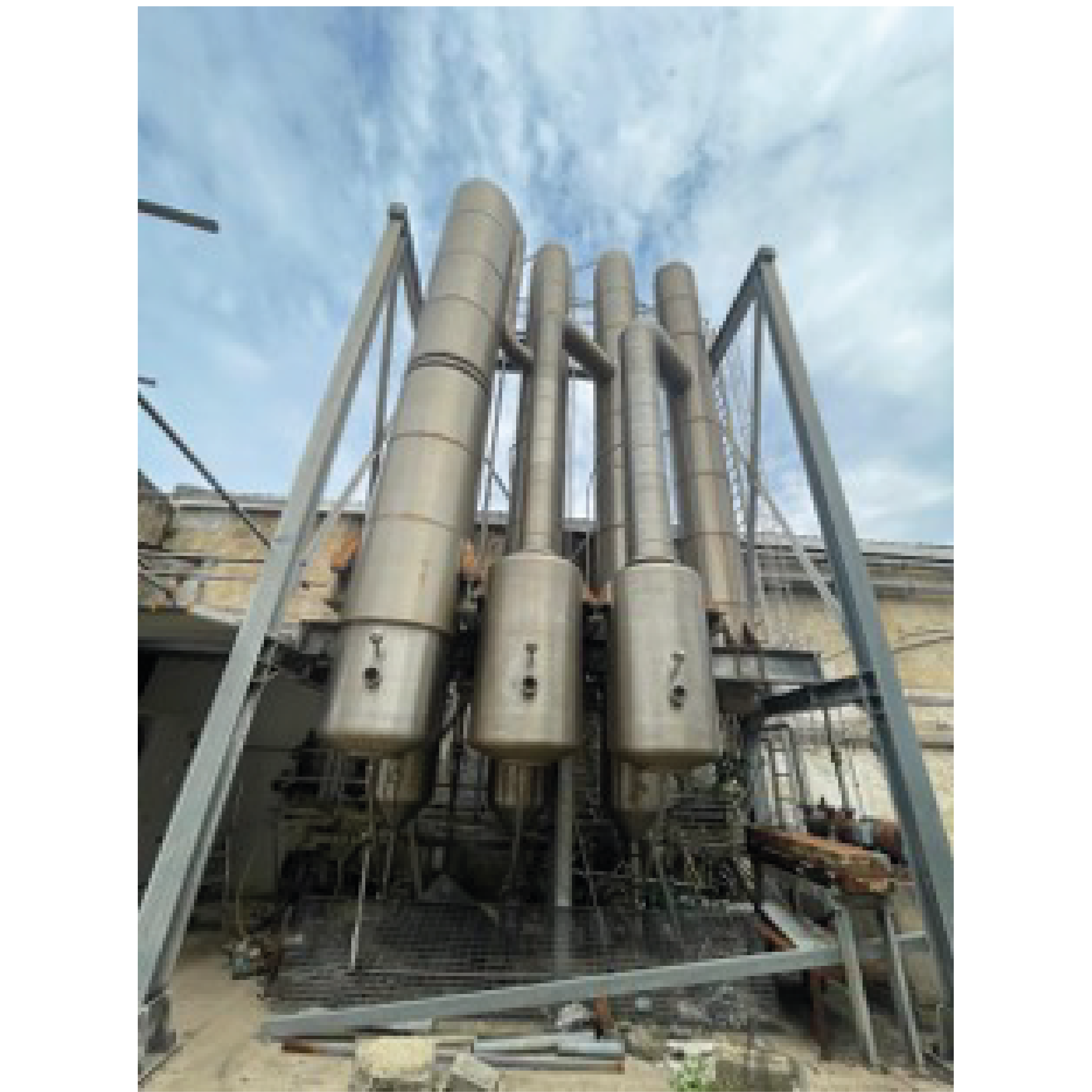
PRIMA

DURANTE
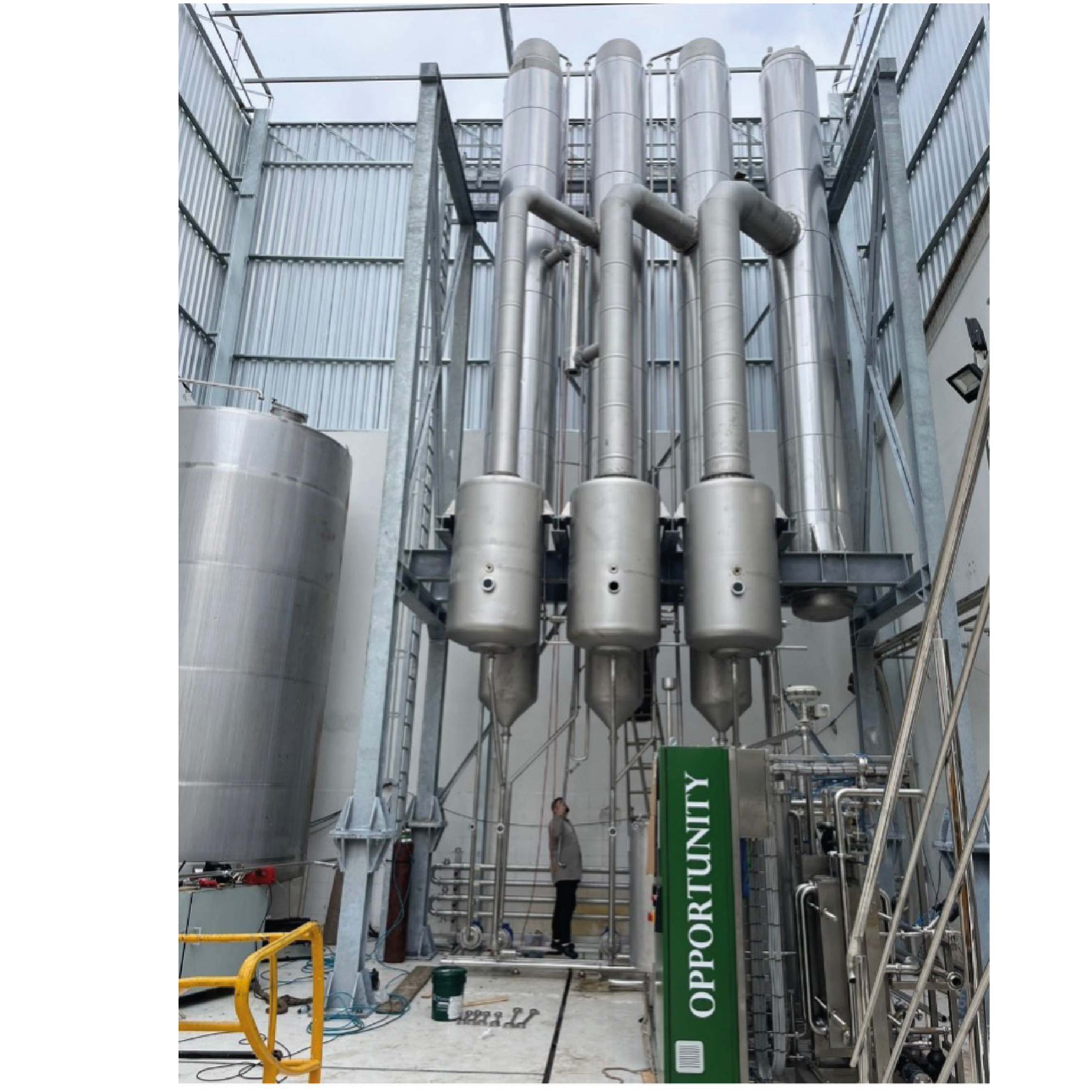