CONCENTRATORE
AZIENDA: ZANLORENZI SÃO MARCOS
PRODUCTO A FABRICAR
Zumo de uva
Empezamos con una máquina usada, que fue completamente desmontada y revisada en su totalidad:
Llevamos a cabo:
- Cambio de la cámara del primer efecto: debido al mal estado de la existente.
- Se realizaron pruebas hidráulicas en las cámaras para asegurar que no había fugas en los ejes de los tubos (partes críticas de la interacción vapor-producto).
- Se realizaron todas las entradas necesarias para el posterior trazado de las tuberías, tales como entradas de vapor, salidas de condensado, salidas de no condensado, adaptación de salidas de producto, recirculación, etc.
- Todas las tuberías se fabricaron a partir de 0 con su respectivo dibujo en 3D, lo que nos permitió facilitar su fabricación.
- Las patas de la estructura se alargaron para poder elevar la máquina en su totalidad para un mejor funcionamiento.
Se desgalvanizó y galvanizó toda la estructura, ya que es el único elemento que no es de acero inoxidable, y para ello se realizaron tratamientos superficiales en el acero para asegurar su larga vida sin pérdida de calidad del material. - Se realizó el premontaje de toda la máquina para su correcta fabricación y conexionado y para evitar dificultades en el montaje de la máquina en las instalaciones del cliente.
Por último, pero no por ello menos importante, se colocaron todos los aislamientos necesarios para aumentar la eficiencia energética y evitar cualquier tipo de inconveniente durante la producción, ya que el acabado superficial dado a la chapa es muy frágil a los golpes.
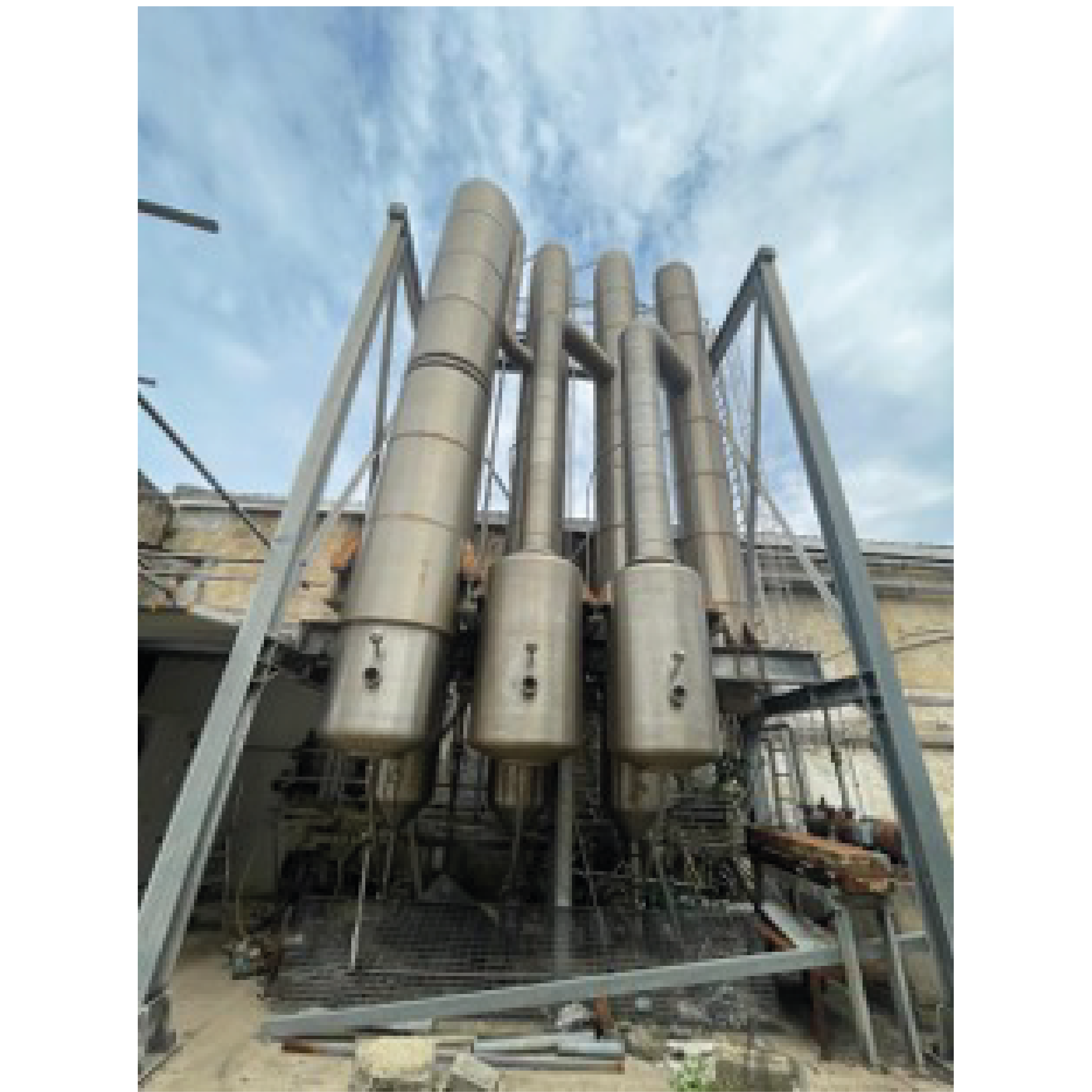
PRIMERO

DURANTE
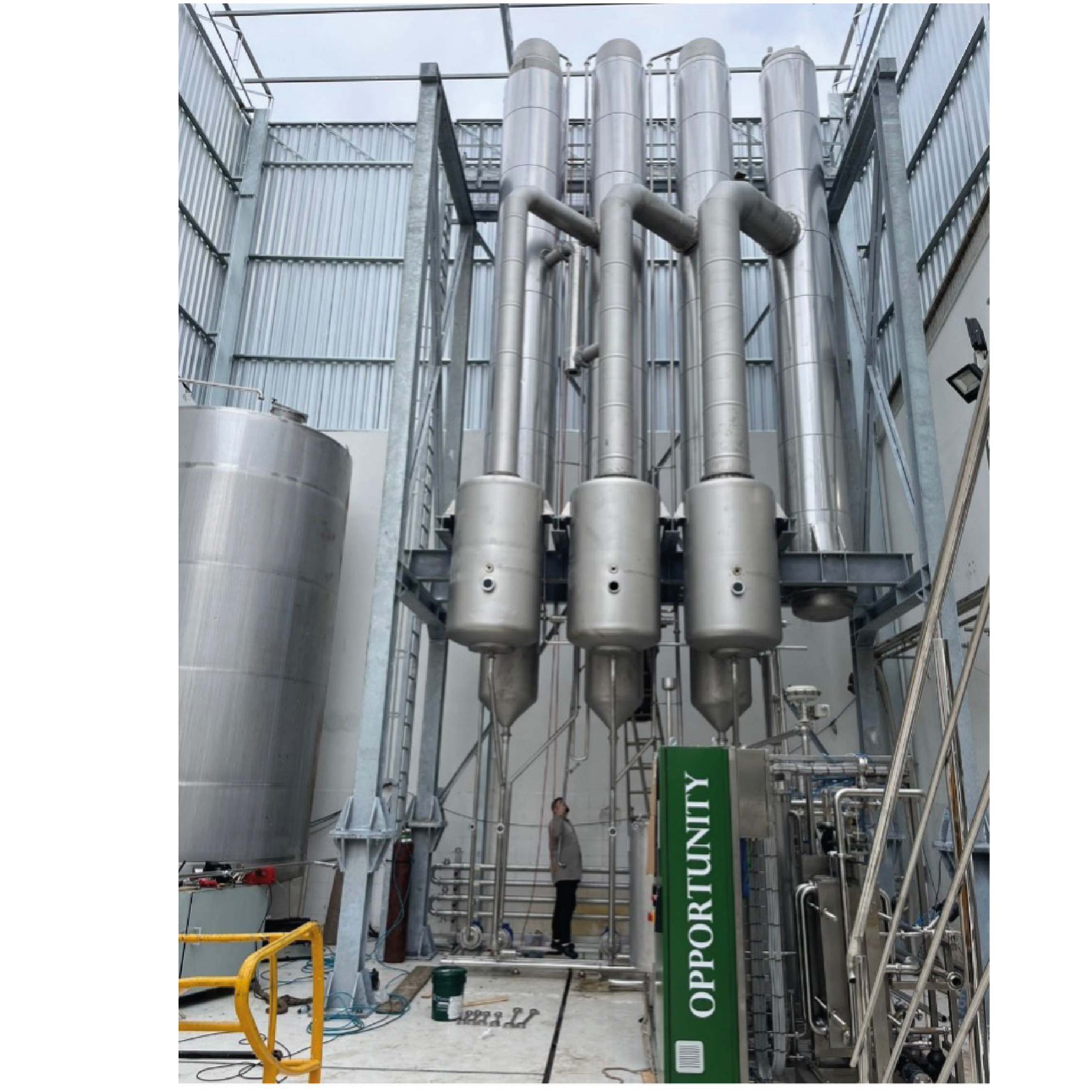