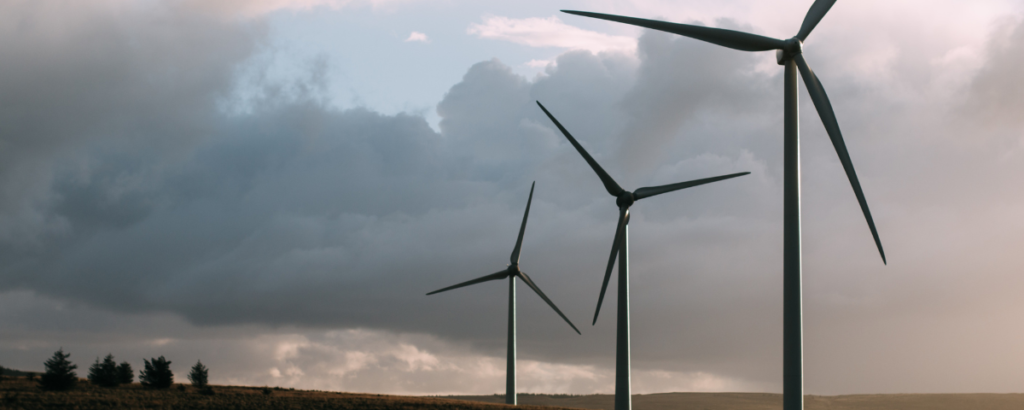
Energy Recovery System in Industrial Machinery: Efficiency and Savings
Energy optimisation is a priority for many companies wishing to reduce operating costs and minimise environmental impact. Energy recovery in industrial machinery is a strategic solution to combine efficiency and sustainability.
In this article we will explore the benefits, operating mechanisms and state-of-the-art technologies related to energy recovery in industrial machinery
What is an Energy Recovery System?
An energy recovery system is a technology designed to capture and reuse energy that would otherwise be lost during industrial processes. This energy may come from waste heat, exhaust gases or mechanical vibrations. Energy recovery allows these resources to be transformed into useful energy, reducing dependence on external sources and improving the overall efficiency of industrial machinery.
How Energy Recovery Systems in Industrial Machinery Work
Industrial machinery generates large amounts of energy in the form of heat or motion. Energy recovery systems intercept this energy, convert it and reuse it. For example, a system based on heat recovery uses heat exchangers to convert heat into electrical or thermal energy, thus reducing the need for additional energy.
Common Technologies Used
- Heat Exchangers: Used to recover thermal energy from hot process fluids.
- Steam Turbines: Convert excess heat into mechanical or electrical energy.
- Kinetic Energy Recuperators: They convert movement into usable energy.
Advantages of Energy Recovery in Industrial Machinery
Implementing an energy recovery system in industrial machinery brings a number of tangible benefits:
- Reduced Energy Costs: Energy recovery enables companies to significantly lower their energy bills by utilising energy that would otherwise be wasted.
- Minimisation of Environmental Impact: By reusing energy, the consumption of fossil fuels is reduced, contributing to lower greenhouse gas emissions.
- Increased Operating Efficiency: Machines that utilise energy recovery systems operate more efficiently, improving productivity and reducing wear and tear.
- Regulatory Compliance: Many governments encourage or mandate the adoption of sustainable technologies. Implementing energy recovery systems helps companies comply with these regulations.
Applications of Energy Recovery Systems in Different Sectors
The adoption of energy recovery varies according to the industry sector and the type of machinery used.
- Food and Beverage Sector: In pasteurisation and distillation processes, heat recovery saves energy and improves the sustainability of production.
- Chemical and Pharmaceutical Sector: Recovery systems are used to re-use heat generated by chemical reactions or drying processes.
- Metallurgical sector: Heat released during metal smelting and machining processes can be recovered and used to heat other parts of the plant.
Emerging Technologies in Energy Recovery
Thanks to advances in engineering and automation, energy recovery systems are becoming increasingly sophisticated. Technologies such as artificial intelligence and the Internet of Things (IoT) are transforming the way data is collected and analysed, enabling more efficient management of recovered energy.
Customised Solutions
More and more companies are opting for customised systems, designed to adapt to specific production needs and to maximise economic and energy benefits.
Challenges and Opportunities in Implementation
Despite the many advantages, there are some challenges in adopting an energy recovery system:
- High Initial Costs: The initial investment can be significant, but the long-term savings more than compensate.
- Regular Maintenance: Recovery systems require careful maintenance to ensure optimal performance.
- Staff Training: The adoption of new technologies requires specific technical skills.
How to Start with Energy Recovery?
To implement an energy recovery system, it is essential to follow a structured approach:
- Energy Analysis: Assess how much energy is wasted and which processes can benefit from recovery.
- System Design: Choose the most suitable technologies according to production needs.
- Installation and Testing: Integrate the system into existing industrial machinery and verify performance.
- Continuous Monitoring: Use analysis tools to continuously optimise the system.
The Future of Energy Recovery in Industrial Machinery
Energy recovery is not just a trend, but a necessity for the future. With the increasing focus on sustainability and efficiency, more and more companies are adopting these solutions. The future will see greater integration with advanced technologies such as automation and predictive analytics, making energy recovery systems even more effective.
Learn more about Energy Recovery
If you are interested in optimising your industrial machinery or want to learn more about energy recovery technologies, keep exploring our blog articles. You will find useful information and updates on the latest innovations to make your company more efficient and sustainable.